BASIC TRANSFORMER PARALLELING CONTROL
I. Introduction
Regards Power. This paper provides an introduction to the Circulating and Delta VAr methods of paralleling load tap changer (LTC) Transformers and step-voltage regulators. There are three premises for transformers operating in parallel:
- The Transformer must continue their basic function of controlling the load bus voltage as prescribed by the setting on the control.
- The Transformer must act so as to minimize the current that circulates between them, as would be due the tap changers operating on inappropriate (not necessarily equal) tap positions.
- Actions 1 and 2 above, must operate correctly in multiple transformer applications regardless of system configuration changes or station breaker operations and resultant station configuration changes.
Of special interest are paralleling operations with the following system conditions:
- The primary windings of the paralleled transformers might be fed from different source transmission lines or
- There is a large variation in relative impedances of the paralleled transformers as tap changes occur.
II. Understanding the System
Referring to Fig. 1:
- A tap difference causes a circulating current (IC)
- IC is calculable from the tap step voltage and transformer impedances
- If C is open = Independent operation – LDC currents assumed equal – no correction needed
- If B or D is open = Independent operation – LDC current doubles – current correction needed
- If A is open = Parallel operation – separate sources (VAr balance required)
- IC is mostly VAr’s since transformer impedances are mostly reactance.
One of the most important facts to consider is that KW flows are not effectively controlled by tap position but by relative impedances or phase shifting transformers.
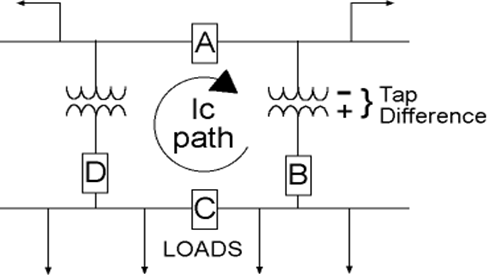
A power transformer has a very high (25 to 50) X/R ratio. That is, power systems in general are reactive and the resistive portion of transformer impedances is negligible. An in-phase voltage change (as in a tap changer operation) applied to a reactive circuit (as in paralleled transformer configuration) significantly changes the transformer VAr flows but not the Watt flows.
Since tap changes do not create changes in circulating KW flow, KW flow must not be a factor in controlling the paralleled tap changers. If system or equipment characteristics (other than tap mismatch) can substantially affect the KW flow through the transformers, VAr flow must be the only determining control quantity. Transformers with directly-connected secondary that supply the load are in parallel regardless of the high side connection configuration.
III. Defining the Problem
In transformer paralleling applications by using, the individual tap changer controls are energized by separate VT’s and separate CT’s. Although these VT’s and CT’s may have the same ratios and specifications, they cannot have identical outputs. Also, while each transformer has equivalent controls, they cannot be identical in voltage sensing and timer operation. Another possibility is that one tap changer may operate faster than another. This leads to the distinct possibility of the operation of one transformer tap changer adjusting a bus voltage while the second does not. Generally, if there was some variation that makes one tap changer operate first, that same variation would cause the same transformer to operate first the next time a voltage adjustment is needed. For these reasons, additional paralleling equipment is required to maintain the taps in the most beneficial position. Following is a description of the operation premises for paralleling methods:
A. The circulating current paralleling method assumes that a continuous circulating current path is maintained for all system operating configurations, and that any changes in the circulating current magnitude are a result of an undesirable change in the relative tap positions of the paralleled transformers. The circulating current method biases all paralleled controls to operate next in the direction that minimizes the circulating current. This is similar to the bias of the LDC unit described in the negative reactance method. Additional equipment is necessary to separate the total transformer currents into a load current portion and a circulating current portion. This is shown in Fig. 2. These individual currents are input to the voltage control which determines the direction and amount of the individual biases. Rather than varying the voltage bias between units based on Vary flow, as in the negative reactance method, the higher-tapped transformer control set point is biased down while the lower-tapped transformer control is biased up by an equal amount. The actual center of the set points of the combination is still equal to the original set point. This assures proper voltage levels are maintained on the bus. An overcurrent relay in the circulating current path is generally used with the circulating current method to block further operations if the variation in the transformers’ tap positions becomes too great.
B. The Var balancing (Delta VAR) paralleling method’s theoretical basis is that paralleled transformers are meant to share the VAr load (as well as the KW load) of the load bus. Since the KW sharing of the paralleled transformers is determined by the relative transformer and system impedances and not the tap position, KW flow should not be able to affect tap position choice. Further, that the best choice of loading parallel transformers is to maintain the VAR sharing regardless of KW loading.
Source side separation, illustrated by Fig. 1 with breaker A open and all others closed, introduces the probable unequal flow of VAr’s and/or KW’s in the two transformers. An equivalent configuration can occur at stations with ring bus or multiple bus breaker arrangements on the source side. This operation violates the assumptions of all methods except the VAr balancing method ( Delta VAR) for maintaining the most appropriate tap positions on the paralleled transformers.
IV. Operational
- Common High- and Low-Side Busses
Referring to Fig. 1, all breakers (A through D) are closed. After adjusting CT’s to compensate for possible different impedances*, circulating current is a function of mismatching tap position operations. Problems can occur if impedance changes in one transformer are substantially different from the impedance changes in the other as tap changes occur. The problem is that the KW (as well as VAr ) loading is changing, as reflected in the circulating current, and KW changes could be a factor in tap positioning for all methods—except the VAr balancing method.
*Note: for equally-sized but different impedance transformers, the adjusting CT’s mentioned above are no longer required when using the VAr balancing method.
- Paralleling Interrupted
Referring to Fig. 1, breakers B through D operate singly or in combination to isolate one transformer from the other. Any paralleling method (except negative reactance) uses “a” or “b” contacts from the breakers (See Fig. 2) To determine this condition and operate appropriately.
- Source Side Separation
Referring to Fig. 1, breaker and opens which separates the sources to the paralleled transformers. Although contacts could also indicate this condition, there is no operating procedure for the standard methods of paralleling for these circumstances.
Before the breaker operation, either KW or VA’s or both could have been flowing from one portion of the transmission system to the other through these lines (or, more load was being supplied by one line than the other). When the breaker opens, the voltages on both lines will reflect the preceding condition by either being at different voltage levels (VAR flow) or different phase angles (KW flow). That is, that flow will attempt to continue through the transformers albeit more limited by the additional transformer impedance inserted into the circuit.
Since tap changes (in-line voltage changes) will not materially affect KW flow in a reactive circuit and a solution which best equalizes the loading of the paralleled transformers is desired, these responses of the different methods to this condition must be considered.
Circulating current method of paralleling—if the intersystem flow was VAr’s, the circulating current method would bias the operation of the tap changers to attempt to offset the flow. This would result in proper operation at different tap positions for the two transformers and proper sharing of the VAr load from the two sources. That is, the tap difference would equal the voltage level difference thus stopping the flow-through Varese this is satisfactory operation.
If the intersystem flow was KW, the circulating current method would again bias the operation of the tap changers to attempt to offset the flow. However, the KW flow cannot be corrected with tap changer operations. The result is fairly unpredictable but does result in circulating VAr’s in one direction and circulating KW in the other. This condition usually results in “hunting” between tap changers.
If the intersystem flow was a combination of VArs and KW, the circulating current method would bias the operation of the tap changers to attempt to offset the flow. This condition could result in “hunting” between tap changers.
With the VAr balancing method of paralleling, since the Delta VAR method ignores all KW flows, it has only one purpose under all system conditions with the transformers paralleled. That purpose is to equalize the transformer VAR flows to the substation load by the appropriate ratio of the size of the paralleled transformers. This “appropriate ratio” is determined by the choice of the current transformer ratios used to correctly parallel differently-sized transformers. Although auxiliary CT’s are not required for equally-sized transformers with different impedances, the total ratios do need to reflect the different sizes of the transformers. For example, if a 100 MVA transformer is paralleled with a 50 MVA transformer, the desired VAr loading ratio is 2. This is accomplished automatically if the CT ratios are different by a factor of 2, which would be normal.
V. Implementation of VAR Balancing Method
Since the VAr calculations are completed in the algorithms of the voltage control, the Delta VAR method uses the same auxiliary equipment as the circulating current method. Namely, a parallel balancing module (which separates the load current from the difference or circulating current) and an overcurrent relay (which gives independent backup protection to the paralleling operation). This makes it a direct replacement for other controls already using circulating current methods. Fig. 2 illustrates those connections for three identical LTC transformers in parallel.
The circuit in Fig. 2 includes the LTC control (the “90” control), the parallel balancing module (the “43” device) and the circuit breaker “a” and “b” contact arrangement. The overcurrent relay (the “50” device) normally used is not shown in this figure but would monitor the circulating current and operate to cut the motor power. The “90” control can be programmed to use either the “circulating current” method or the “ΔVAR” method of paralleling. It is a straightforward extension of this schematic to apply to either the two transformer or the multiple transformer paralleling application.
Current magnitudes as drawn in Fig. 2 assume a 1500 ampere unity power factor load on the system. There is a reactive current of 35 A in T1 because it is on a tap position higher than T2 or T3. Because we assumed a unity power factor load, it is easy to distinguish the control circuit currents which are due to the load (the real components) and those due to circulating current (the reactive components). As expected, the load current portion is accommodated independently within the control circuit of each transformer, whereas the circulating current interacts between the controls. In this illustration, there is twice as much current in the paralleling input to the 90 control at T1 as in those on T2 and T3. The T1 control set point bias will be biased down twice as much as T2 and T3 are biased up transformer or the multiple transformer paralleling application.
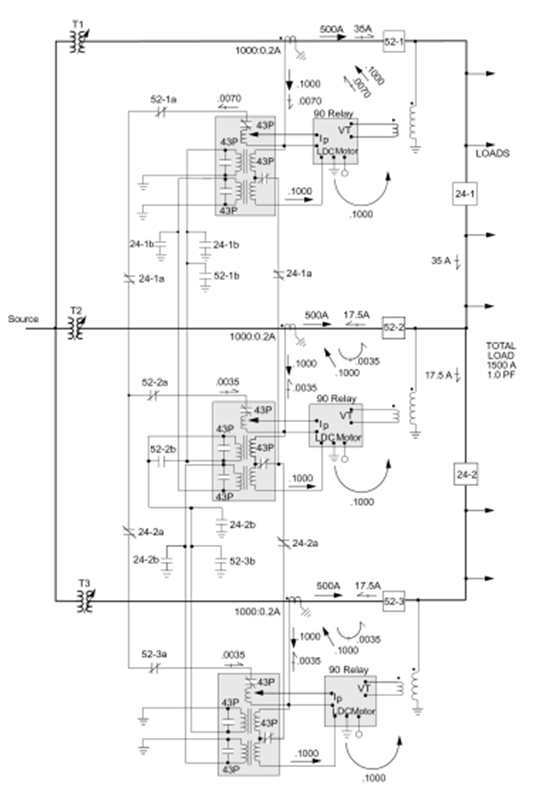
VI. Digital Tap Changer Control
Beckwith Digital Tapchanger control can be used for paralleling LTC Transformer Control by using Current circulating method or Balance Delta VAr method. Beckwith Digital Tapchanger Control M-2001D used as control No. 90 in Figure 2.
Beckwith’s Tap Changer Control line uses an innovative concept in new transformer or regulator applications or control replacements by using a universal Tap Changer control – the M-2001 – with interchangeable adapter panels. The replacement panels are sized to correspond to the original manufacturer’s controls, use the same mountings, and include wire harnesses that match the existing connections – all for easy replacements. The M-2001’s easy installation, its comprehensive communication capabilities and its variety of features that meet all types of applications have made this control very popular in the industry.
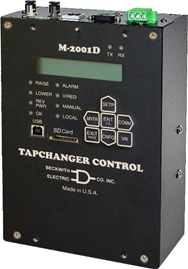
General specification as following of M-2001D:
- LTC transformer, substation regulator, and line regulator control provides reliable operation with expanded capabilities
- Adapter panels to retrofit popular industry tapchanger controls
- USB Communications Port for quick field‑updatable programming
- Smart Reverse Power detection/operation with VT configuration for source and load sides
- Demand metering/Data Logging with Date/Time Stamp (Single/Three‑Phase)
- Harmonic Analysis
- LDC with R & X or Z‑compensation
- SCAMP (SCADA Controllable Auto/Manual Pushbutton) Adapter Panel Auto/Manual Switch State can be changed by a SCADA command
- Sequence of Events Recording
- SCADA HeartBeat
- Smart Flash SD Card
- Source PT Voltage Input
- CBEMA Monitoring
- Cyber Security – Comprehensive cyber security tools to implement NERC CIP requirements, including IPsec and RADIUS server security
- VAr Bias for downstream coordination with capacitor controls
- Tap position knowledge by four KeepTrack™ methods
- Transformer paralleling by circulating current, Master/Follower (peer to peer) circuitry, or ∆VAR® methods
- LCD display (rated ‑20 to +70 degrees Celsius) or Vacuum Fluorescent display optionally available (rated ‑40 to +80 degrees Celsius)
- Optional Control Power Backup Input for Fiber Optic communication loop‑through
- DNP3.0, MODBUS® and IEC 61850 Communications Protocols available
- Optional Ethernet RJ45 or Fiber Optic Ethernet
May be Useful.